One, who pays for the future
In 2004, the size of China's beverage market reached 24.49 million tons. The rapid growth of tea, juice, and functional beverages in particular continued to provide opportunities for hot-filling PET bottles. If the PET bottle adoption rate of 60% and the PET bottle standard of 1000ml are estimated At least there will be more than 10 billion PET bottle needs.
Beer, on the other hand, is a matter of technical research and consumer psychology. In addition to preservation, sterilization, and other issues, whether consumers can accept plastic bottled beer is still an issue to be verified. People expect to have 3.5% PET bottled beer in 2005. Obviously, compared to 0.1% in 2002, this is a worthwhile attempt.
Second, PET bottle blowing technology
"The relevant person in the employment China Bottlenet believes that the production of packaging machinery and PET bottles in China is far behind the development of beverages." In the field of blowing bottles, China's current development is mainly a two-step process because the efficiency of the two-step method is relatively high. From the blowing point of view, foreign countries have reached more than 50,000 bottles per hour, or even more than 70,000 bottles, just 25,000 bottles in China.
Mr. Zhang Zhong, Asia Pacific president of Sidel believes that the one-step market in the world is declining and the two-step process is growing. There are two main reasons. The first is that the current bottle preforms can be purchased everywhere. Commercialization is very common; the one-step growth at that time was a factor in that customers had no way to find a suitable preform in many places, but now due to the mass production of preforms, customers can easily obtain preforms without having to produce their own. . The second is that the two-step method has advantages over the one-step method in both cost and quality. In the blow-molding market, the cost of packaging bottles is extremely sensitive, and two crucial factors determine the return on investment: the capacity of the machine and the volume of each blowing station. Sidel's concept of a "dual cavity" (opening a double mold cavity in the same mold), blowing two bottles simultaneously at the same station, is ideal for large-scale production of small containers. Sidel's SB020 second-generation dual-cavity device yields up to 60,000 bottles/h.
Olaf Weiland, managing director of SIG Corpoplast, believes that “Every manufacturer in the future will produce the containers he needs in his own factoryâ€. Obviously from the perspective of economic benefits, transporting empty bottles to filling plants will increase costs. Now the beverage industry's production is from bottle blowing, filling and packaging to improving overall line efficiency. The two-step method has the advantages of light weight, simple operation, and flexible production. It can directly use bottle embryos without taking into consideration many issues such as PET raw materials, and concentrates on the final product filling and other aspects. Mr. Chen Juntian, Director of China, introduced SIG Corpoplast's blow molding machine, which has a short die change time. The output of each cavity can reach 1,630 bottles per hour, which is very fast.
Krones' Contiform H40 stretch blow moulding machine can produce thermoformed bottles and standard bottles. The output of 500ml bottles is 44,000 bottles/h, which is suitable for hot filling PET bottles.
Third, the affection of green leaves to the root
Bottle caps are a detail that is often overlooked by consumers, but for manufacturers, this is a big problem. Mr. Li Keping of Italy's Jetflex has many years of research on bottle caps and cap moulds. “Manufacture of plastic caps looks simple, but the manufacture of plastic cap moulds has a very high level of expertise.†Jetflex is known for designing and manufacturing multi-cavity, high-precision, hot runner injection molds. In 2000, Jetfield developed a 64-cavity rapid-mold cap mold, and achieved a 3s opening and closing on the Nestal rapid injection molding machine, creating a world record for 64-cavity-grade cap mold opening and closing cycles. “Many manufacturers of plastic caps in Europe are seeking to reduce the weight of caps and increase productivity in order to reduce costs and increase market share while ensuring the physical function of the caps.†The company developed MIVA in response to market demand. Series bottle caps. Take MIWA L3P as an example, 28mm, only 1.5 ~ 1.6g, 1g lighter than the traditional PET bottle plastic cap, this cap can be opened as long as the rotation 90 °, opening torque is low, suitable for young and old. At present, there are seven sets of 64-cavity cap molds provided by Jaffit Corporation for use in the Wahaha Group. Jetflex also invented a patented technology for non-rotating two-shot injection molds for the single-use production of liner caps. This invention greatly saves the investment in the production equipment of the capped bottle cap. Conventional production of padded caps is achieved by injection caps, injection or dis- placement devices, and assembly equipment. With Jaffier's two-shot injection molds, adding an injection unit to the original injection machine is a breeze. The realization of the production of cushioned caps.
Sacmi SACMI's pressed cap is another technology. Unlike traditional injection caps, it is the first mechanical manufacturer to bring press-molded capping equipment to market. The Sacmi rotary hydraulic press makes the mold simple, so the investment cost required for compression molding is far less than the injection molding cost. Since Sacmi completely designs and manufactures plastic cap moulds at the same time, it has a greater overall advantage. According to Sacmi's introduction, this pressed bottle cap is very suitable for the production of round caps. Sacmi exhibited 600/min cappers at the ProPak in July, but their fastest products reached 1200/min, and 7 of them are currently sold.
Injection molding and pressing of bottle caps represent two different processes. The former can buy various molds, perform a flexible design, and can design relatively complex lids, but the cost of the molds is higher; and the pressing of bottle caps is relatively low cost.
Bericap is a German family-owned company that specializes in bottle caps. It has 18 subsidiaries and has sales of 310 million euros in 2003. The Kunshan company in China was established in 1998. In China, it mainly supplies 30/25 and PCO 28-mouth caps, 38mm, 48mm and five-gallon Tamper Evident caps. And functional caps (such as bottled water anti-theft caps). It produces approximately 900 million 30mm bottle caps for the "non-carbonated drinks" industry in China. The current "Ballige Service Pack" is a new form of packaging that has been studied together with users and has gone far beyond the design of standard bottle caps. For example, in the 38mm hot filling field, the SK 38/16 DoubleSeal hot fill bottle cap is the ideal solution for large-scale equipment for efficient filling.
Taiwan Yanxin is a company affiliated to the Master Kong Group. It is also an expert in food and beverage packaging caps and preforms. Its innovative KingCan caps can be used for various refillable or non-recyclable daily packaging such as glass bottles and plastic bottles. Cartons and metal containers are available with caps, as well as a variety of caps with or without gaskets; colors can be varied, with monochrome to 4-color top printing or embossed to facilitate branding; and PET bottle mouth provides patented inner plug seal cap design and manufacture.
Challenge the ubiquitous air
PET bottles have the advantages of good transparency, chemical stability, good barrier properties, light weight and low cost, and can be recycled. However, there are three types of PET bottles that require barrier properties: First, O2-sensitive juices and dairy products and vials. Carbonated beverages; second, products containing CO2; and third, products that are sensitive to O2 and contain CO2, such as beer. As beer bottles, the barrier properties of PET bottles have been severely tested. Beer packaging is the most demanding of all drinks. This is why less than 0.1% of the 250 billion beer containers in the world used PET bottles in 2002.
The first is the compressive strength, which can prevent the exudation of CO2 under high pressure and the infiltration of external O2; followed by the heat-resistant strength, it must be able to withstand the high temperature of pasteurization; and the third is the impact resistance. Improving the barrier properties of PET bottles has become the main direction for major companies. This involves raw materials, equipment, processing techniques, and modification of PET.
Currently, barrier technologies are mainly embodied in several aspects. The first is the surface coating method. For example, Sidel's Actis technology adopts amorphous carbon coating, which has a 30-fold increase in oxygen barrier effect compared to ordinary PET bottles. The cost is only 78% of glass bottles and 65% of metal cans have obvious advantages in recycling. Its Actis 20 plasma coating machine can handle 10,000 0.6L PET bottles per hour. Sidel had promoted Actis coating technology in China in 2001, but at that time, the popularity of PET bottles in China and even the world in the beer market was clearly overestimated. But today is different. The young people born in the late 1970s are almost grown up, holding and carrying PET bottles, and the degree of recognition has been greatly improved; Actis-coated PET bottles are very picky in Germany. The beer market has achieved high acceptance rates for customers and consumer goods. Mr. Paul Holderith, executive vice president of Sidel Group, believes that the opportunity to promote in China has come, but Sidel will look for partners to promote. There are many pioneering companies in the beverage industry in China, so the space for win-win is very high. Big. Arne Andersen, Plasmax Coatings Equipment Manager at SIG Corpoplast, told reporters that Plasmax coating equipment uses PET Plasma Chemical Vaporization and Sedimentation (PIVCD) technology to produce PET-filled bottles. This plasma technology uses two gases to mix and ignite the gas to produce a chemical reaction that coats the inner wall of the PET bottle with SiO2. This coating is completely transparent and does not change the color of the original PET bottle; the coating can be cleaned with chemicals and completely recovered; since the coating is inorganic, it does not react with the product, thus ensuring safety. According to Andersen, coated PET bottles cost about $100 more per 1000 bottles than uncoated ones; but if you select a coating, you can reduce the thickness of the PET bottle wall, reduce bottle weight, and thus reduce bottle production costs. . Plasmax 12D coated bottles and systems, coating speeds of 10,000 bottles/h for PET bottles of various sizes (0.4 to 1L).
The technique of vacuum plasma enhanced chemical meteorological deposition has been strongly supported by Japanese companies. This diamond-based carbon treatment process DLC was mainly developed by Japanese Nippon Essby ASB, Japan Kirin Beer, and Mitsubishi Corporation. This coated DLC film PET bottle has more than 20 times more O2 barrier performance than a regular PET bottle and 7 times more CO2. The transparency is very high, the coating is soft, it is not easy to crack, and it has strong acid and alkali resistance. Currently it is developing corresponding production equipment and advancing to the Chinese market.
The barrier silicone coating was developed by Coca-Cola and Krones and other companies in Germany to develop barrier-enhancing silicon-treated PET bottles, which are more economical than using PEN bottles or multi-layer coated bottles. However, this coating may cause the outer PET bottle to fill with needle-like holes; TetraPak, Switzerland, also developed plasma-coated SiO2 technology in the PET bottle to form a glass-like barrier coating with a thickness of 0.1 to 0.2 mm on the inner wall of the bottle. Layer, canned beer with this bottle, the shelf life can be extended to 4 to 12 months. It can handle 18,000 0.2-2L beer bottles per hour.
Other coating technologies such as SIPA of Italy, SIPA, use PPG's epoxy-amine barrier coating to produce PET-epoxy-amine coated PET bottles to form a bright scratch-resistant barrier; Tetra Pak DOW Chemical Company's thermoplastic ring resin uses two layers of bottles to adjust the thickness of the barrier layer; DuPont, DuPont, also develops two-stage coating technology that can increase the barrier to O2 and CO2 by more than 30 times.
In addition to spraying the barrier layer technology, the hybrid material modification method is combined with multi-layer co-extrusion molding technology, and the market is rapidly developing. Add other substances in the PET bottle, such as PEN, LCP, MAX6, etc., to form a new plastic packaging material. This method includes material blend modification, copolymerization modification, multilayer composite modification, and nano-scale PET plastic (NPET). Zhuhai Zhongfu Industry Group, a company that dares to innovate, is the leading domestic PET bottle production company and is the earliest manufacturer of PET bottles approved by Coke. They use multi-layer composite modification and use PET bottles made by the multi-layer co-injection process provided by Kortec Co., which can withstand high temperatures of 67°C. The shelf life of beer can reach 6 months; Canadian HUSKY company provides barrier properties for production. In the method of bottle multilayer preforms, the gas barrier layer is made by co-extrusion blow molding and final embryo separation.
Krones's barrier coating, such as BestPET, can process single-layer PET bottles with a capacity of 20,000 bottles/h and industrial applications in beer, juice, tea beverages, soft drinks and perfume containers.
Filling Competition
In 2001, the market revolution opened the curtain with a unified "fresh orange" hot-filled PET bottle juice drink; while Huiyuan imported PET aseptic cold filling line to regain its leading position in the juice beverage market, and its annual processing capacity exceeded. One million tons, to reverse the decline, which "he + her" with the help of excellent marketing, four months of sales to the front.
Aseptic cold filling technology of PET bottles can reduce the cost by reducing the weight of PET bottles, but the investment cost of aseptic PET equipment is very high, the cost of one line is more than 10 million euros, and the environmental sanitation requirements for the plant Very high. There are about 200 domestic filling and processing machines, and there are less than 30 machines and complete sets of production capacity. The highest domestic filling capacity is only 36,000 bottles/h, while foreign countries have reached more than 70,000 bottles/h. Basically, the domestic hot-filling line is the main, only Lok Hui and other limited manufacturers can provide cold-filling line technology. When the price of PET particles is flat, coupled with the design of molds for heat-resistant PET bottles and the improvement of equipment technology, the advantages of aseptically filling empty bottles can be gradually reduced when grammage is further reduced. Mr. Mei Jun of Sidel Company told the reporter that the real test is from milk-containing tea beverages (such as milk tea, coffee milk, etc.). These production lines must use sterile PET bottle filling lines.
The mature beer market is declining. The key to getting out of the downturn is to promote product quality and breakthrough packaging methods. SIG-Simonazzi developed a new beer sterilization process to achieve the long-term preservation of the stable quality of PET bottled beer, namely the enhanced pressure cold sterilization EPT, which uses high pressure at high speed (according to pressure gradient) for already filled plastic bottled beer. Water treatment and semi-insulating rapid heat treatment combined sterilization. This EPT process is characterized by the fact that the already filled beer product is directly applied to the product and packaging materials (bottles and lids), thus eliminating secondary contamination during the filling process.
Mr. Chi Zongbo of Guangzhou Lehui Company believes that it is possible to fully draw on the advantages of cold filling in foreign countries and develop aseptic cold filling lines suitable for China's national conditions. If the Krones model is used in the sterilizer, the air quality in China is poor, and secondary pollution is likely to occur during the blowing and conveying process of the bottle. The Krones model can effectively sterilize the inside and outside of the bottle; the bottle washing machine should use KHS. The three-channel mode makes it easy to adjust, if the disinfectant is not completely sterilized, it can be added with a disinfectant to sterilize the bottle rinsing machine; the PROCOMAC mode is selected in the structure of the filling valve, because the domestic gap in the rubber sealing materials is currently larger. Sri Lanka and KHS's solenoid diaphragm valves have high requirements for diaphragm seals, while Procomac selects aseptic tanks for use in aseptic cans, which are simple in structure and use non-intrusive, non-hermetic filling to reduce moving parts. The cost of operation and maintenance is effectively reduced; the cleanroom is designed by Procomac and the equipment is operated through isolation and the operating environment is low. Lehui's aseptic cold filling line has been running in Beijing Huiyuan, and can be used in 350-2,500ml PET bottled high-acid, low-acid and neutral fruit and vegetable juices, teas, and various beverages, keeping the taste of the beverage and maintaining freshness. , reduce the cost of packaging materials up to 1/2 to 1/3. Since the bottle does not have to withstand high temperatures, it is free to design the bottle type without worrying about the heat deformation of the bottle (this is very important for marketing considerations).
However, the cold or hot filling line is not a key factor in determining the market. For example, Weiquan, which belongs to Dingxin Group, is a hot-filling process. However, its cold chain is used for storage and transportation. Its taste is still very good. East China market sales have been good. Therefore, content is actually the most critical factor in winning consumers.
Labeling technology
In the filling line, the technical content of the labeling machine is relatively high, and the domestic market is still in a monopoly position of foreign brands. At present, only the Guangdong Pinghang Machinery Factory can keep up with the development of the market. From a market point of view, Mr. Liang Wei, Manager of SIG Alfa Alpha China, believes that on the one hand, the labeling machine must flexibly adapt to the needs of customers on the premise of the speed of operation and the speed of the filling machine. On the other hand, it reduces costs. The request. From the technical point of view, Mr. Robert Krones's labeling technology department, which is in the leading position in China, believes that the direction of the labeling machine is a component labeler, and the same machine can satisfy several different labeling methods. Ms. Feng Jianxin, China Manager, mentioned Krones' new direct-sleeve Sleevematic DS and Sleevematic DS Inline in-line direct-sleeve labelers that can eliminate the need for vacuum and reduce cleaning.
The performance of the Sacky labeler Opera is excellent. Its scroll labeler can continuously and effectively work at 60000 bottles/h. It can label empty and real bottles, and even label light bottles of less than 13g. Also suitable for the latest label material (18mm OPP or PET), no difference in use with other materials. The biggest problem with previous labeling machines was the efficiency of the bottling line. Users often arranged two or three labeling machines to work in parallel. In particular, in the rolling labeling process, there are often two or three machines. When linearly arranged machines work on the same line, this is obviously a waste of money. The scroll labeler has a good guarantee on efficiency and speed, and is suitable for shrinking labels. Currently, Sacmi is conquering the labeling on non-vertical bottles and the high-speed technology of stickers.
Recycling technology
In addition to the physical methods, chemical recycling has attracted increasing attention in PET bottle recycling methods. Australia's Petecycle pty's penew patented technology is in use, and the device can handle 100kt PET bottles. The process is to treat colored or coated PET bottle waste by steaming the PET bottle with ethylene glycol for 1 hour to embrittle it, and then grinding it to 1mm size to remove impurities and alcohol. The solution is an oligomer, including some terephthalic acid monomer; after a special filtration process to remove pigment additives or coating impurities, the final product can be obtained in the existing device and fresh monomer mixture, esterification can be made colorless PET bottle.
Looking forward to brilliant
In recent years, the plastic packaging market has grown rapidly and the average annual output has increased by over 11%. PET bottles have contributed to this. Just as Mr. Chen Zhijun, president of SIG Beverage Machinery, believes that although the cost of PET packaging remains unresolved, due to the rich shape, improved processes can increase the shelf life, ease of transport, preservation and recycling, and the future in China.
Candy Printer Equipment characteristics
1) High precision EPSON nozzle, printing color and delicate, not fade and fade.
2) Intelligent RIP technology, double nozzle white color printing at the same time and printing speed is so fast.
3) Intelligent automatic cleaning device, no need to manually draw the ink; using a real small ink droplets 3PL printing
4) Fashion design is simple, easy to operate, ect
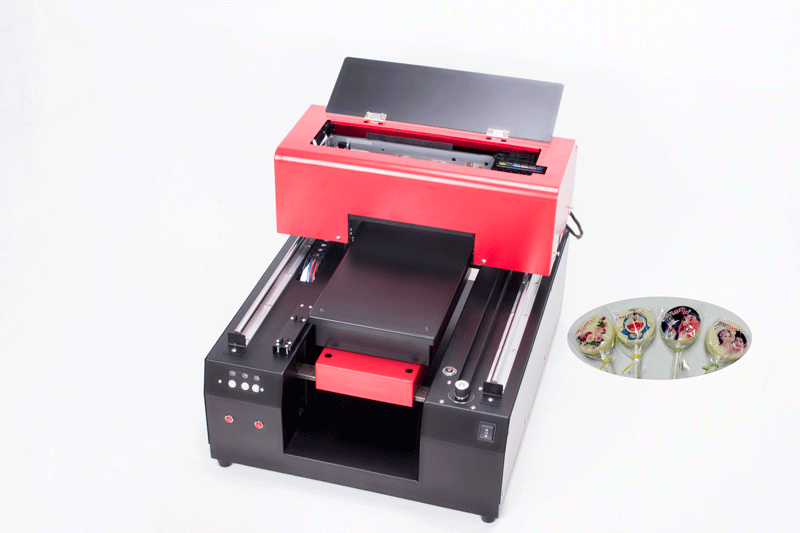
Name
|
Candy printer
|
Print head
|
DX5
|
Print size
|
21*38cm
|
Print color
|
CMYK+LC LM
|
Print speed
|
A4 photo/163s
|
Printing resolution
|
5760*1440dpi
|
Nozzles
|
90*6=540
|
Interface
|
USB 2.0
|
Net weight/Gross weight
|
35kg/42kg
|
Printer size
|
57*48*44cm
|
Height adjustment
|
Handle/Automatic
|
Working power
|
110-220 50-60Hz 30W
|
Operation system
|
Windows 2000/XP/WIN7/Vista etc.
|
Temperature
|
5-35º
|
Candy Printer
Candy Printer,Automatic Candy Printer,Digital Candy Printer,Candy Cake Printer
Shenzhen Refinecolor Technology Co., LTD. , https://www.rfcprinter.com